(August 4, 2023)
The supply chain crisis created profound international issues, sparking product shortages and serious shipping
backlogs.
East Tennessee State University’s Dr. Matthew Jenkins, an assistant professor in the
Department of Management, Marketing and Supply Chain, helps explain what happened – and why.
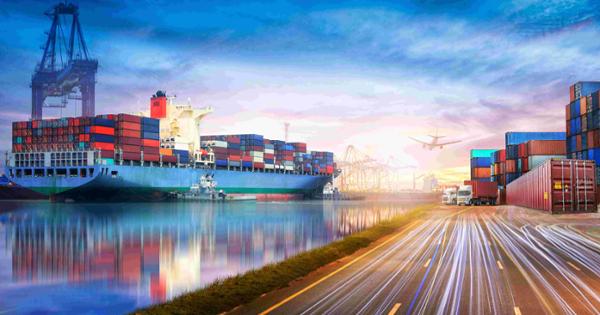
“Factories, ports, machines, et cetera are difficult and expensive to build and maintain.
Obtaining a return on investment for these resources requires achieving high utilization
rates, meaning that there is very little excess capacity to absorb any kind of sudden
fluctuations in demand,” he said. “While this helps to make the system more efficient,
it also makes it much easier to overburden the system.”
The COVID-19 pandemic helped ignite the crisis. But there were signs of a looming calamity before 2020.
“Even prior to the COVID supply chain crisis, supply chain experts were warning the
industry that capacity was dangerously overutilized and that a significant demand
shock would cause catastrophic issues in certain industries,” he said. “In the case
of COVID, when economic shutdowns occurred, consumer demand patterns shifted quickly
and unexpectedly.”
Other events made the crisis worse.
For one, while companies anticipated softening demand for consumer product, demand
for homes, construction materials and more significantly increased. That paired with
factory shutdowns in China – the largest exporter of physical goods in the world –
resulted in major backorders.
Companies like UPS and FedEx suffered considerable strain, too, as consumer preferences
changed quite suddenly. Many Americans, thanks in large part to COVID-19, shopped online in force.
“These issues were further exacerbated by difficulty in finding and hiring drivers,
distribution center workers, other service personnel, shipping containers and other
transportation equipment to facilitate these deliveries,” he said. “The transportation
and distribution system were not able to add capacity at the rate that demand had
increased unexpectedly.”